How Is Molded Pulp Packaging Made?
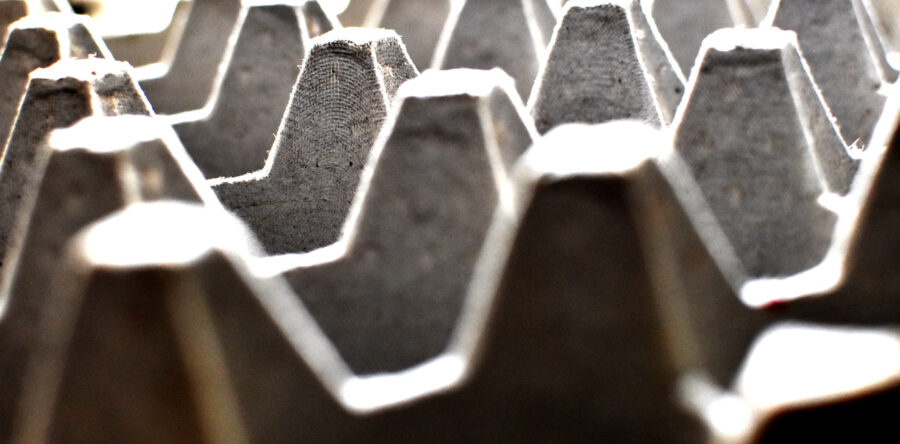
In 2022, the market for molded pulp packaging was valued at 5.11 billion USD and it is anticipated to expand at a CAGR of 7.6% from 2023 to 2030. The main drivers of this market expansion are the growing demand from application industries such as healthcare, food packaging, electronics, food service, and others, as well as the increasing demand for environmentally friendly and sustainable packaging solutions. Despite that, not many people are aware of the process used to make this sustainable packaging. Continue reading to find out more!
How Is Moulded Pulp Made?
Molded pulp (also known as molded fiber) container is constructed from fibrous materials like recycled paper, cardboard offcuts, or natural fibers (bamboo, sugarcane bagasse, wheat straw). These raw materials will affect the packaging's surface texture, color, and physical qualities.
Manufacturing molded pulp packaging requires several stages.
First, the raw materials are mixed with water to form a pulp slurry. A mesh forming tool is then lowered into the pulp slurry tank. A vacuum pushes the slurry through the mesh tool until the proper thickness is attained.
Wet parts are removed from the mesh tools and dried. Meanwhile, the dry ones are deformed and bumpy.
The parts are pressed by hot metal tools to polish the surfaces. At this step, debossed logos or artwork may also be used.
Lastly, any holes or windows are die-cut and the edges are trimmed. The end result is a lightweight, sturdy, and versatile packaging material that is suitable for protecting items during storage and transport.
Unlike standard folded cardboard boxes, molded pulp packaging features rounded edges and intricate three-dimensional forms. When the pulp parts are created, they must be released from the forming and pressing tools, thus sharp 90-degree angles are not possible. Rather, pulp packaging is created with 5-10 degree draft angles and corner radii.
What Are the Benefits of Moulded Pulp Packaging?
One of the most important advantages of the molded pulp container is that it is a sustainable packaging option. It decreases the demand for new resources and trash because it is created from recycled paper. It may also be disposed of in an ecologically responsible manner as it is biodegradable and compostable.
Another benefit of a molded pulp container is its versatility. It may be molded into a number of shapes and sizes, making it appropriate for packaging a wide range of items. Further, it is lightweight, which lowers shipping costs and lessens the carbon footprint.
Have you ever desired to have packaging that precisely matches the specs of your products? Molded pulp is incredibly easy to form into various shapes, making personalized product packaging for your business a reality and surprisingly economical.
Last but not least, molded pulp packaging is less expensive than other traditional packaging materials. While the initial investment in equipment and molds might be high, the low cost of materials and the flexibility to reuse molds still make it a cost-effective alternative in the long term.
Final Thoughts
With its improved design, pulp packaging is now employed for a variety of purposes. Global consumer brands like Apple and PUMA created unique and elegant retail packaging with molded pulp. The iPhone is constructed with a smooth white pulp insert placed within a printed rigid box. So this post has explained how molded pulp is manufactured and its several advantages. If you want your business to benefit from this packaging, have a look at our products.